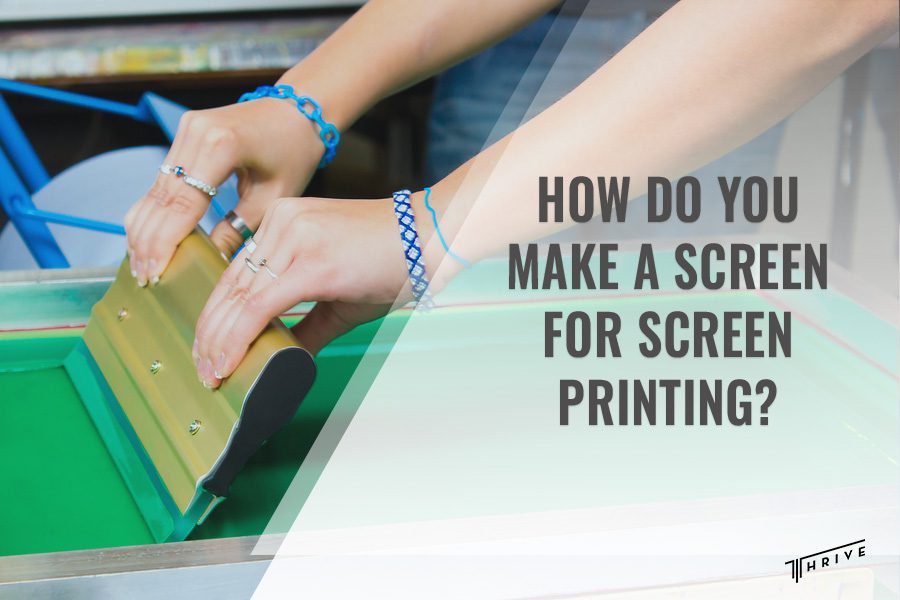
Screen printing is a way to get your favorite designs on all sorts of stuff, like T-shirts, posters, and mugs. Creating a screen involves a series of relatively simple steps that you can master with a bit of practice. So, how do you make a screen for screen printing, and which tools will you need?
The screen is a vital part of screen printing. It allows you to reproduce your design with precision and consistency. Whether you’re printing on T-shirts or other materials, the screen is what recreates your image onto the desired object.
The article provides you with some industry insight to make your printing tasks easier and more enjoyable.
How Do You Make a Screen for Screen Printing?
Being in the printing industry for so long, we have accumulated a great deal of knowledge and expertise that we’re excited to share. People often ask us questions like how to burn a screen for screen printing or how to solve common printing issues, and we’re quite happy to share.
Screens can be used on fabrics, plastics, metal, and paper. It’s essential to have a well-prepared screen to achieve a clean and sharp print on such a broad range of surfaces. A well-made screen with a good stencil will allow for the ink to pass through cleanly and create the images with the desired quality.
If you need custom apparel for your team, choose us to get top-quality prints that stand out from the others. Here at Thrive Screen Printing, we specialize in turning your unique ideas into stunning reality with the industry’s best screen printing printers.
Make your own screen
These steps will guide you in creating your own screen and preparing it for a printing project. The advantage to making your own screen is not only in the cost-saving side but also in the creative freedom it will provide you with. The hands-on DIY approach can be particularly rewarding for hobbyists and screen printing enthusiasts.
Here are the materials you will need:
- Four wooden pieces for the frame
- Screws or glue
- Screwdriver or drill
- Mesh fabric (polyester or nylon)
- Mesh adhesive or staple gun
- Measuring tape
- Square tool
- Clamps
Here are the steps to making a DIY screen:
1. Make the frame
The screen frame is the foundation of the screen as it provides the necessary support for the mesh to remain stretched tightly without any slack or looseness. The frame makes sure there’s an even tension throughout the mesh and allows for precise printing.
Of course, you can always skip the part of making your own frame and repurpose a frame of an old wall painting that fits the measurements. To make a wooden frame, you will need to measure and cut the pieces of wood and make corner joints before attaching them together.
Attach the shorter pieces to the longer ones to form a rectangular frame, and ensure the corners are square with a square tool. After that, secure the corners using screws or glue and make sure that the structure is sturdy and all pieces are tightly connected. Finally, trim any excess or rough edges to create a smooth frame.
2. Cut the mesh
Cut a piece of the mesh fabric and make sure that it is larger than the frame you built to provide you with extra material around the edges. You can trim excess mesh after firmly attaching the fabric to the frame.
When it comes to mesh, the standard mesh count in screen printing is 110 and 156, meaning that 110 or 156 threads are woven per inch of the screen. The higher the mesh count, the more detailed your print will turn out. However, when printing, you will also need to choose the right emulsion and exposure type to match the level of detail.
3. Attach the mesh
You can do this using mesh adhesive or a staple gun. With adhesive, you will need to apply a thin and even layer to the frame before carefully placing the mesh over the frame. You can use a flat object to smooth out the mesh and allow the glue to dry once it’s done.
If you’re using a staple gun, you can lay the frame on a flat surface and attach one side of the frame with the piece of mesh. Then, you must stretch the mesh tightly across the frame and staple the opposite side. Afterward, you must repeat the process for the remaining sides using clamps to hold the material tightly and not create bubbles.
So, this is an easy and time-saving process for making a screen for your screen printing. In the following, we’ll guide you on how you can screen print with the DIY screen you’ve made.
Screen Printing Procedure
To make a screen-printed product, you will first need a few essential materials and tools. These tools are easy to acquire and work with, as they’re readily available at most craft stores and online, while the process itself doesn’t require any complex machinery or expertise.
Let’s put your screen to work!
Materials for screen printing
- Screen
- Screen printing emulsion
- Ink
- Transparency film
- Substrates
- Squeegee
Screen
The screen is the foundation of screen printing. Screen frames can be wooden, aluminum, or steel, and choosing the right frame is important for achieving the best results.
Wooden frames are most suitable for small-scale projects and are a good choice for beginners. Aluminum frames are favored in high-volume projects for their lightweight nature and durability, while steel frames provide the necessary robustness in industrial printing.
Screen mesh is usually made of polyester or nylon and comes in various mesh counts. A higher count allows for more detail in the print, and you should choose it based on the level of detail and the type of material you’re printing on.
Screen printing emulsion
The emulsion is a light-sensitive substance that gets applied to the screen to create the stencil for your design. When exposed to UV light, the emulsion hardens in the exposed areas, leaving the design open for ink to pass through during the printing process.
Emulsions can be water-based or solvent-based, and choosing the right one is important as it will determine the quality of your screen printing project.
To briefly explain, the water-based emulsion is eco-friendly and cleans up easily, but it might not give a sharp image. In contrast, the solvent-based one gives a sharp image, but it’s harder to clean up and not that eco-friendly.
Ink
The material you’re using has to be compatible with the ink. Water-based inks are suitable for fabrics, while plastisol inks are more versatile and work on various surfaces. Specialty inks can add some unique effects to your prints, like glow-in-the-dark or a metallic finish.
Transparency film
Acetate or transparency film is a vital element during the screen printing process. It is a see-through plastic sheet that’s coated on one side for inkjet or laser printing. Transparency film is used to create a transparent copy of the design for it to be printed later onto the substrate of your choice.
It works by blocking the UV light during the exposure process, which allows the light-sensitive emulsion on the screen to harden only in the areas designated by the design. Transparency films are reusable, i.e., you can use them for multiple print runs with the same design. This makes them a cost-effective and eco-friendly choice for screen printers as they save a lot of time and materials.
Substrates
They are the materials onto which you can apply your screen-printed designs. They can vary in terms of type, and choosing the right substrate will come down to the specifics of the project, the intended use of the item, and the type of ink that will be used.
Textiles are the most commonly used material, as T-shirts are some of the most in-demand printing products. Other substrates include paper, ceramics, glass, wood, metal, etc.
Squeegee
Squeegees, as an essential part of the screen printing process, pushes the ink through the screen and onto the substrate. Squeegees are made of rubber, polyurethane, or neoprene. The most commonly used squeegees are 70 durometers having a medium hardness.
The printing process
Once you have the right tools and materials, you can start screen printing to bring your designs to life:
1. Prepare the screen
Before applying the emulsion and diving into the screen printing process, it’s important to ensure that there are no particles on the screen that could interfere with the coating. Inspect the frame you made for any irregularities one final time, and look out for splinters and rough edges that could cause problems.
Put the screen on a clean, leveled, and stable surface to help with the evenness of the emulsion.
Finally, you need to fasten the screen and make sure that it is secured tightly to prevent it from slipping or any movement during the application of the emulsion. We encourage the use of clamps and hinges to help with the stability of the screen.
2. Applying emulsion
You need to coat the mesh screen evenly with emulsion using a squeegee and let it dry in a dark environment. The emulsion will harden and form a thin, solid layer on the screen, which will be the canvas for your design.
3. Image transfer
First, print your selected design onto a transparency film and make sure it’s opaque. This means that the areas of the design where ink should pass through must be fully black to block UV light effectively.
4. Exposure
Expose the screen to UV light using the light source at your disposal. This will harden the emulsion in the areas where the design on the transparency film blocks the light.
5. Rinse the screen
You need to carefully rinse the entire screen with water to wash out the unexposed emulsion. Be careful to avoid washing away any hardened emulsion or damaging the screen in the process.
You can start by rinsing from the back of the screen to dislodge the emulsion more effectively before moving to the front of the screen. Sometimes, you may use a brush to scrub out the unexposed emulsion.
This will reveal the stencil and allow the ink to pass through where the design is.
5. Printing
Now that your screen is ready, you can proceed to set up the printing press, apply ink to the screen, and, using the squeegee, transfer your design onto the desired material.
Conclusion
Screen printing is a technique that allows you to transfer designs onto different surfaces. The article explains how do you make a screen for screen printing and provides a comprehensive guide for acquiring the right materials and tools for making a good screen.
Making your own screen makes the screen printing process easier and more efficient. The screen printing technique is known for its ability to produce vibrant colors and precise details. As a popular choice, it’s great for custom apparel and promotional items because of its durability and versatility.
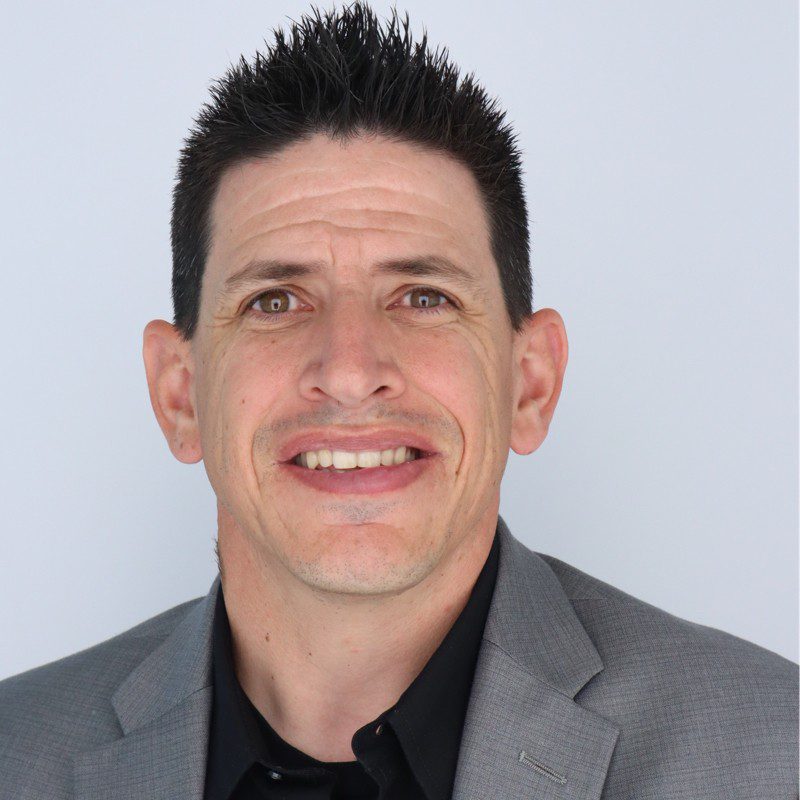
Robert Fisher is the founder and CEO of Thrive Screen Printing and brings extensive experience in the screen printing and fulfillment industry.