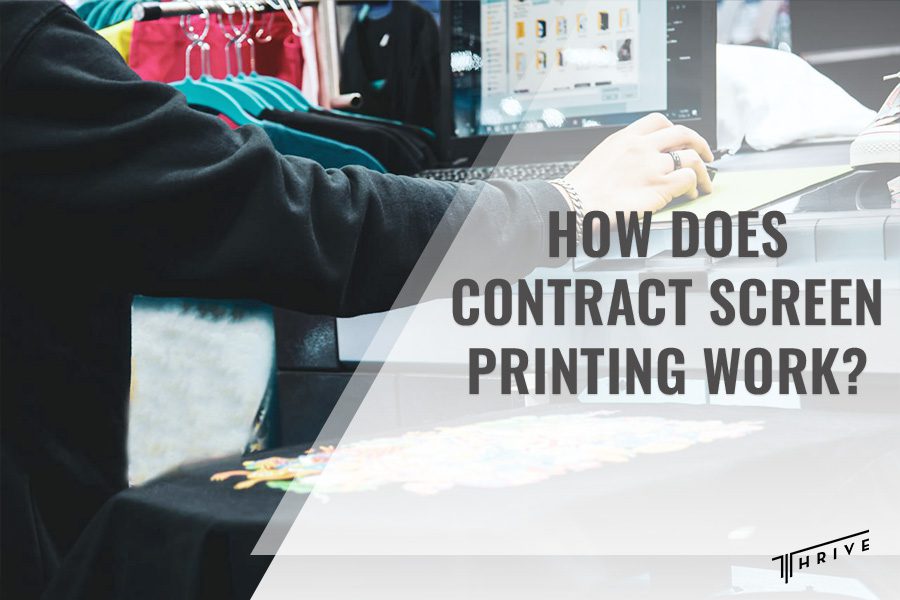
Screen printing is the process of putting a customer’s design onto a T-Shirt. But, there are two types of screen printing: retail and contract. So what is the difference between the two? How does contract screen printing work?
Unlike retail printing, which can include an order of one or a few pieces, contract screen printing means the order is significantly larger. So if you have a significantly larger order, the print shop where you put it may not have the facilities to handle it.
This means they subcontract a contractor for the job. At Thrive Screen, we print both licensed and unlicensed designs.
How Does Contract Screen Printing Work?
If you are looking for someone to handle Contract Screen Printing, you are going to search for a specialist screen printing company. This is precisely what we are. At Thrive Screen, you can send us your designs to screen print.
Contract screen printing involves one print shop subcontracting the actual printing to another shop. Generally, contract screen printing happens due to the order’s size, design type, difficulty, etc.
Print shops and retailers usually utilize contract sprinting due to:
- Speed – the main focus of contract printing is speed. The customer submits the design or artwork they want printed, and the printers fulfill the order as fast as possible.
- Setup Times – contract printing companies reduce setup times to the lowest possible. All of the mechanisms and steps are set up for maximum efficiency
But screen printing for us is more than just the technical side of the business. We enjoy helping our clients bring their artistic visions to life. Art is at the core of our company.
The Reasons for Contract Printing
Printers providing contract printing services, like us, offer specialized skills to customers that retail screen printers do not have. The reason why businesses like retailers, companies, and organizations prefer to use contract printing are the following:
- Specialized printing technique – contract printing companies often have special techniques and methods to set them apart in a highly competitive field
- High-volume orders – printing shops that do not have the capacity to handle high-volume orders subcontract them to shops that offer contract printing
- Lower pricing – because contract printing involves higher-volume orders, contract printers generally print at lower costs than retail printers
Process of Contract Screen Printing
Our team helps you let your creative juices flow and prints the design you dream up on a large scale. At Thrive Screen, we can handle a large-scale contract screen printing operation. Daily we can produce and ship out 20,000 items.
Screen printing on such a large scale requires a team dedicated and highly knowledgeable of the finest details involving the procedure steps.
With our team of 50 specialists, our clients can rest assured that they get high-quality items we print, label, package, and ship to them. The steps involved in contract screen printing are the following.
Design creation
Unlike other contract companies that only print your design, we are here to help guide you even through the design process. Once you show us the artwork you want placed on your garments, our team will walk you through the design process.
They will explain everything from material selection to helping you choose the best printing method to bring your design to life.
Screen preparation
After you finish with your design creation, the next step in our printing process is screen preparation. Our professional printers will choose a suitable mesh screen according to the complexity of your design and the type of fabric you choose.
Afterward, we place the sheet with the design onto an emulsion-coated screen. When developed under bright light, the mesh screen will harden. The bright light only hardens the emulsion, while the parts of the screen covered by your design stay in liquid form.
Once hardened, we wash off the emulsion to remove any unhardened bits, leaving a clear design imprint. After the screen is dry, the stencil is ready for use.
Item preparation
Next, we put the item (t-shirt) onto the printing board while the screen is on the printing press above the item. We use five automatic M&R Presses and two manual ones for contract screen printing.
If the design is multicolored, it will require color layering. Automatic presses can layer color in fast succession.
Ink application
The most commonly used ink for screen printing is plastisol. But as our customer, you can pick from the top ink varieties available today. The print can look softer to the touch, depending on the type of ink used.
Different ink can also enhance the 3-D effect or create a unique sheen to the design. The ink we offer besides plastisol are:
- Gel printing
- Foil printing
- Flock printing
- Metallic ink printing
- High-density printing
To apply the ink, we lower the screen onto the printing board. The ink goes on the top end of the screen, and a squeegee pulls it along the entire length of the screen. This application technique presses the ink through the open areas of the stencil, printing the design on the item.
After all the items are printed, the emulsion is removed from the mesh screen with a special washing fluid.
Drying and curing
After printing the items, we pass them through a dryer to cure the ink. This technique creates a smooth and colorfast finish. Once all the items are dry, our finishing team will add the labels.
Quality control
The last step before we package the items and send them out for shipping is quality control. All printed items must pass quality control; if there are any issues, we remove and print a new item in its place.
We take great pride in our work and only provide the highest quality service to our clients. After the items pass our quality control, we package them and send them on their way to you.
Final Word
Ultimately, how does contract screen printing work?. The short of it is that print shops like ours have the capacity to handle large orders, so other shops, companies, and retailers contract us to handle them.
As one of the longest-standing contract printing and finishing companies, we offer customers high-quality and speedy service.
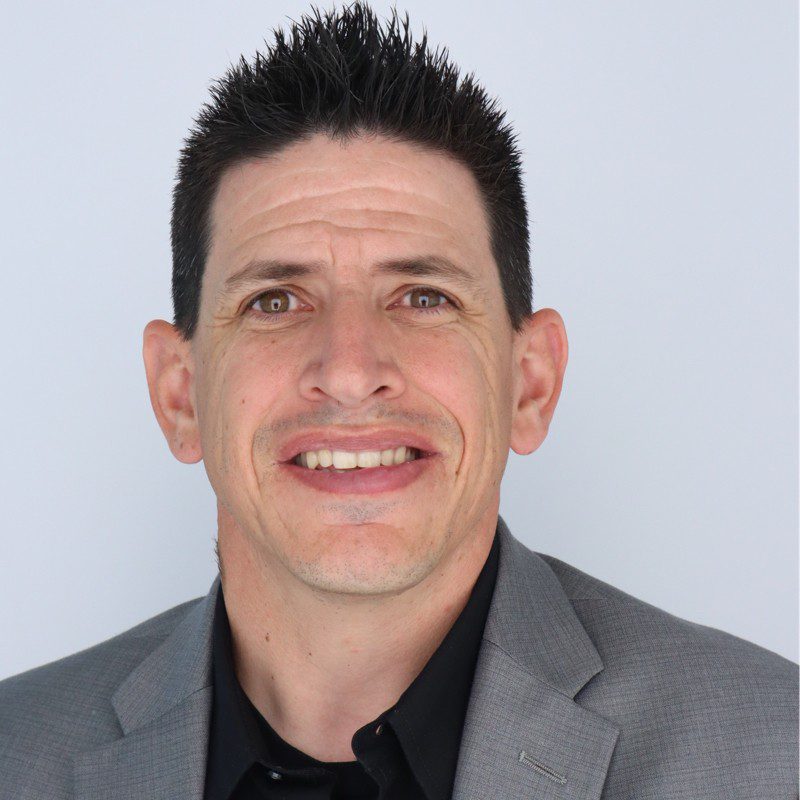
Robert Fisher is the founder and CEO of Thrive Screen Printing and brings extensive experience in the screen printing and fulfillment industry.